Rollers
Before rubber and polyurethane, people used rollers made from materials like wood and metal which were strapped with rope or animal skin. It was only after the discovery and understanding of how to vulcanize these elastomers during the industrial revolution that these rollers would become weather resistant, chemical resistant, water resistant and elastic.
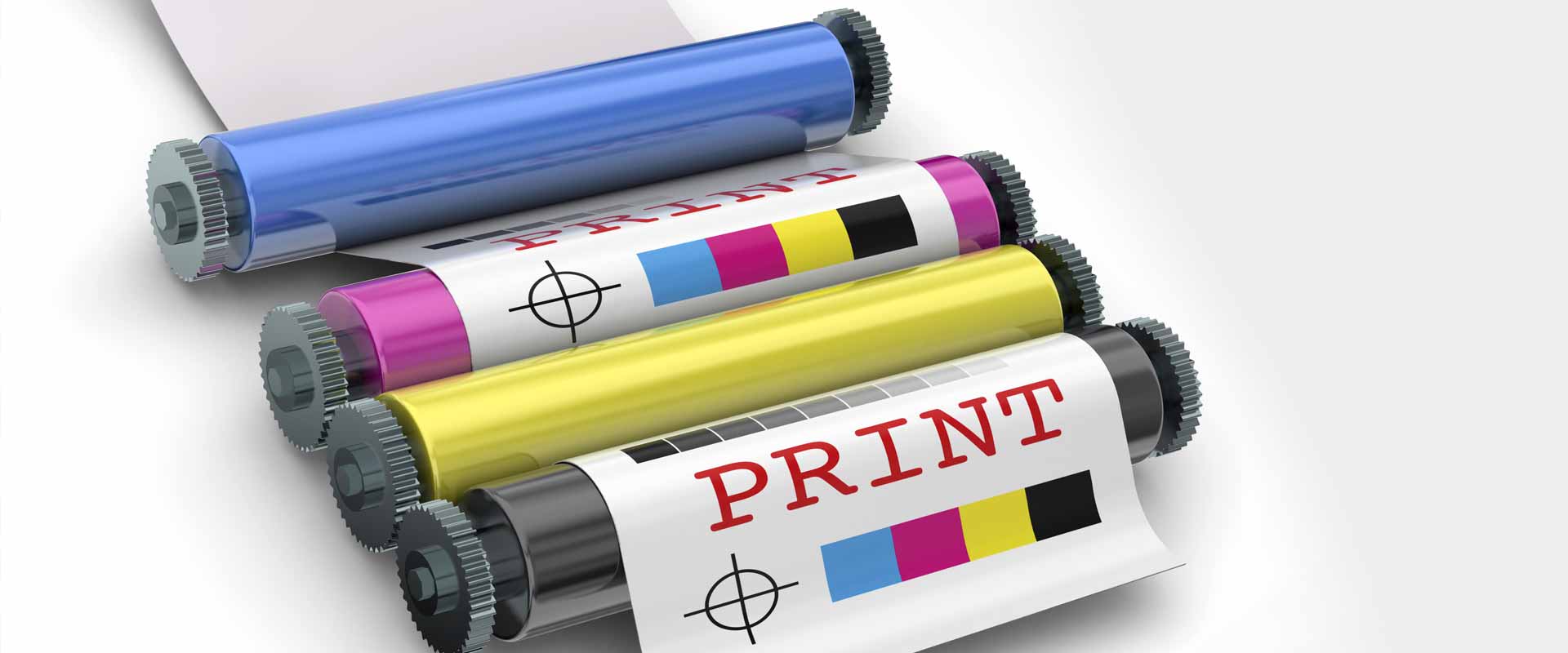
Background of Industrial Rollers
With the understanding of how to vulcanize industrial rollers, research engineers experimented with the process and were able to control the hardness of the rollers. This helped publishing and printing industries to start using rubber rollers to spread thin glue layers and apply ink to their printing plates.
Since the early discovery, industrial rollers have become more durable, sturdy and long lasting and are used in a wide array of industries in
their processes including coating, drying, annealing, calendaring, embossing, metal processing, heat treating, packaging and bulk material handling.
Research and development have resulted in better elastomer performances creating unlimited application possibilities, resulting in exponential growth in the roller industry. Demanding application requirements and focused research has given rise to new synthetic polymers such as Polyurethane, Silicon, Nitrile, Neoprene and EPDM.
Process
Molded rollers can be processed by injection or compression molding, depending on the type of polymer used and the product that is manufactured. Molding process commonly involves a hydraulic press and a die. The die gives the shape to the raw rubber, whereas press provides pressure and heat to cure the rubber product. The process begins by filling raw rubber into a metal mold, and then a hydraulic arm fitted with a die presses the mold and provides heat and pressure. After a set time the pressure is released and the product comes out taking the shape of the mold.
Casting rollers are produced by injecting liquid polymer into a cast mold, this cast mold is then put in a hot oven. The high temperature in the oven helps the castable liquid to cure and take the shape of the cast mold.
In both the process when metal cores are used, the metal (Aluminum,
Mild Steel, Stainless Steel ) needs to be treated before the molding or casting process begins, this is done to ensure proper bonding of the polymers to the metal core. As a standard procedure the metal cores are processed to remove any impurities on its surface, such as oil or rust as this will weaken the bonding between the polymer and metal. After the metal surface treatment, a bonding agent, usually made of polymer-solvent solutions, a primer coat and a top final coat is applied to the metal. The next step involves surface treatment, this is done by grinding the rollers to the finished diameter that is required by the customer. In many applications, grooving is required on the rollers. There are a number of grooves that can be created on a surface of rubber, including square, trapezoidal, “V”, double edge saw, half circle, and round. Moreover, on a rubber roll, these grooves can be made vertically, horizontally, helically, worm, diamond cut groove and screw threaded.
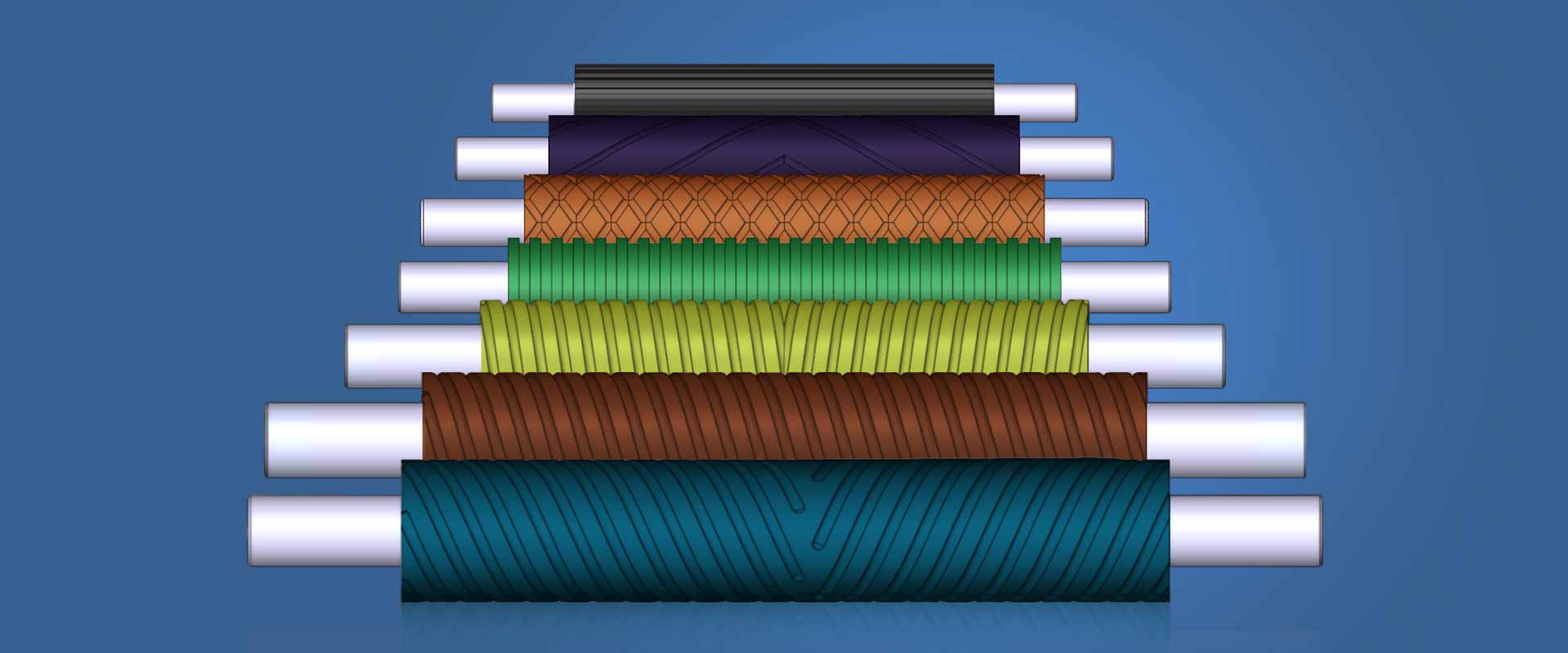
Features Advantages & Types
Polyurethane / Rubber rolls feature a polyurethane / rubber outer covering and a metal core. They typically feature grooves, which offer a variety of possible uses depending on the application, such as: increasing the amount of coating, smoothing wrinkles out from a paper or plastic film, preventing belts from slipping in a conveyor system, embossing surfaces, helping to release heat created by friction and adding texture to rubber rolls.
Polyurethane / Rubber rollers offer their users a wide range of advantages.
- First, unlike metal rollers used in conveyor system, they have high coefficient of friction, which provides great traction in moving parts and components.
- Also, rollers can compensate for small changes emerging from machine functions.
- In addition, these rollers offer all of the advantages of rubber itself.
- The reason that polyurethane / rubber are such a popular material for making rollers and assisting object movement is that it can be repeatedly compressed and relaxed without losing its shape.
A material that could not hold its shape, which would need constant replacing, would be virtually useless.
In addition, they can absorb shocks and resist and protect against damage and scratching.
Industries Served

Types of Rollers
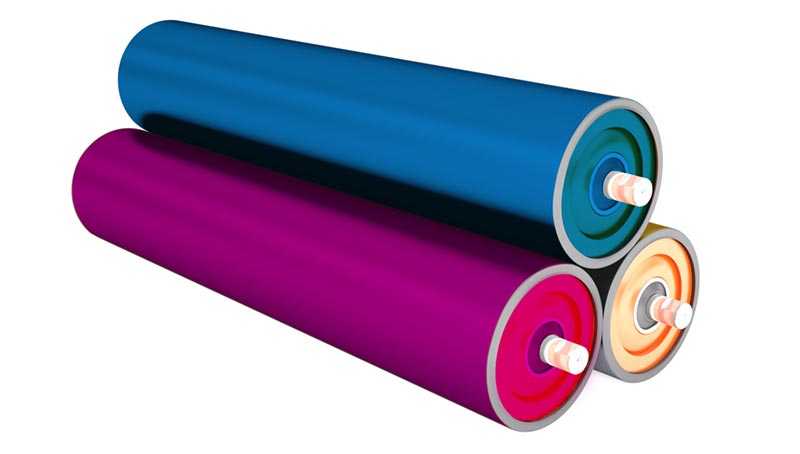
Ink rollers
Ink rollers also called printing rollers, apply ink to paper and other materials; rollers may contain ink within themselves or they may be engraved with a pattern.
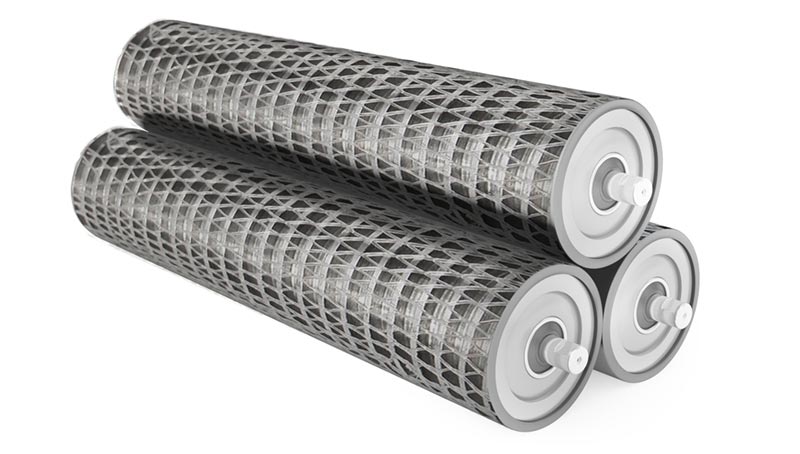
Laminating rollers
Laminating rollers, made of heat resistant materials like silicone rubber, are heated up to 500°F to laminate materials on both a small and large scale.
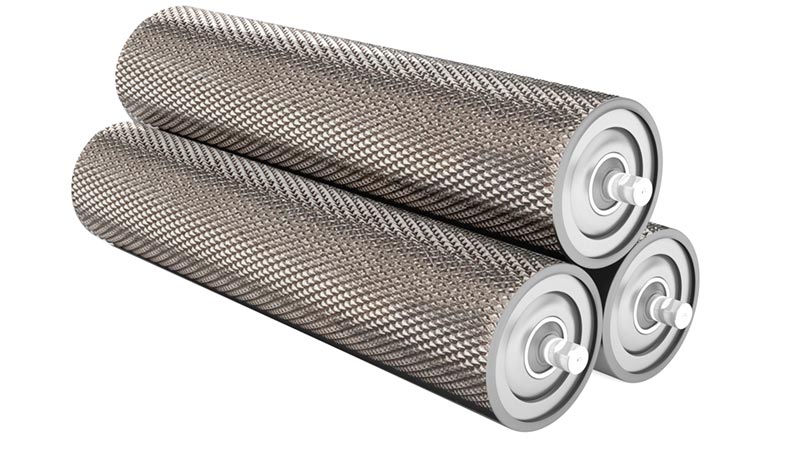
Drive rollers
Drive rollers are movement focused rubber rollers. Often used for converters and web machines, they operate using integral shafts equipped with keyway that acts as a gear.

Grooved rollers
Grooved rollers are called so because they have a grooved pattern, usually a spiral, U or V; grooved rollers are usually part of moving systems like belt driven conveyor systems.
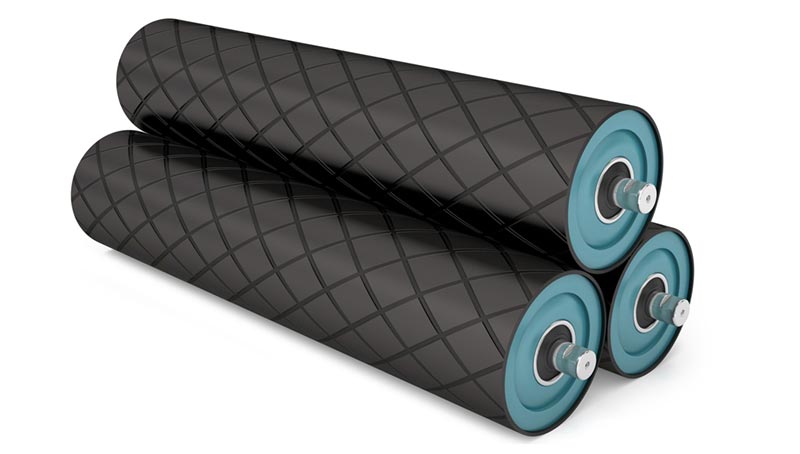
Guide rollers
Guide rollers, or idler rollers, provide support to other roller systems like conveyors, but they do not actually move anything.
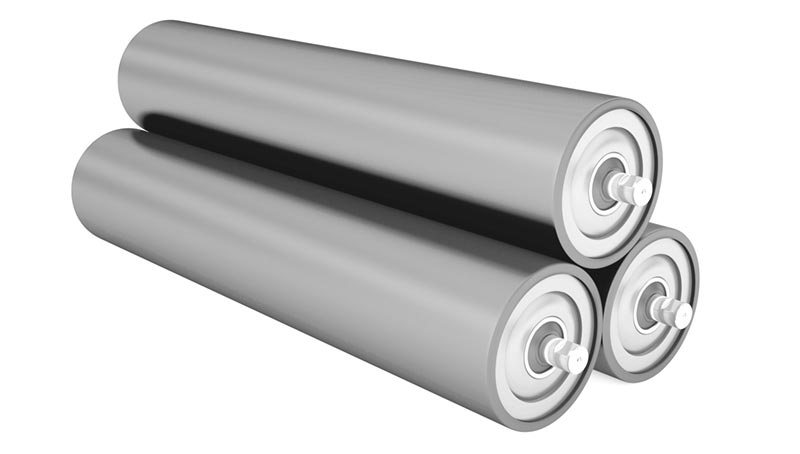
Conveyor Rolls
Conveyor rolls, or conveyor rollers, simply move, or convey, materials.

Industrial rubber rollers
Industrial rubber rollers are rubber rolls used in industrial applications, primarily manufacturing machines like: stamping presses, conveyor systems, bending machines, printing presses, and the like.
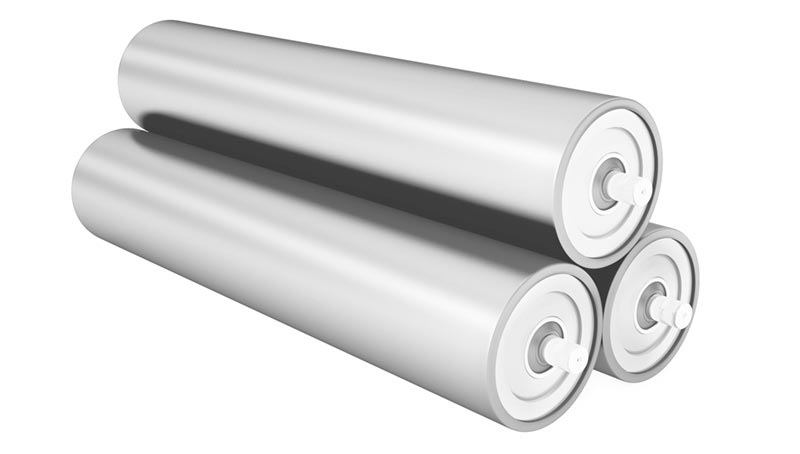
Live shaft roller
Live shaft rollers are designed to withstand difficult environments and high load quantities; they have external bearings in which both the roller shaft and the roller rotate.
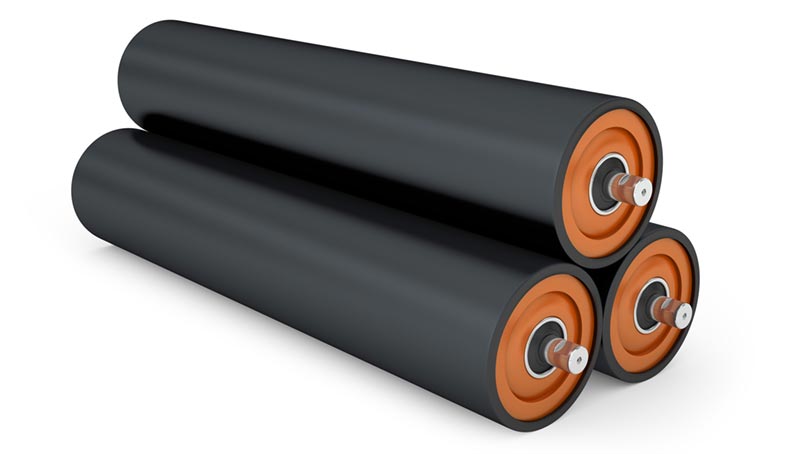
Stinger rollers
Stinger rollers, finally, are configured very much like dead shaft rollers, but they are designed specifically for marine applications.
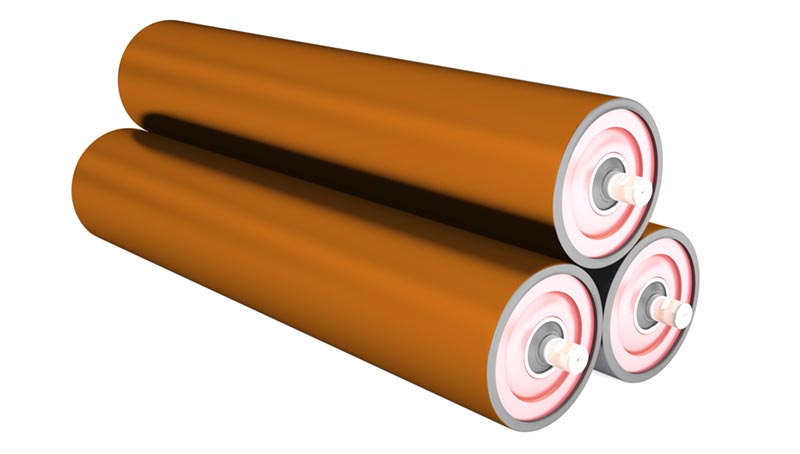
EPDM rollers
EPDM rollers are heat resistant, corrosion and oxidation resistant and weather resistant, and are thus quite versatile. However, they do not hold up well against petroleum products.
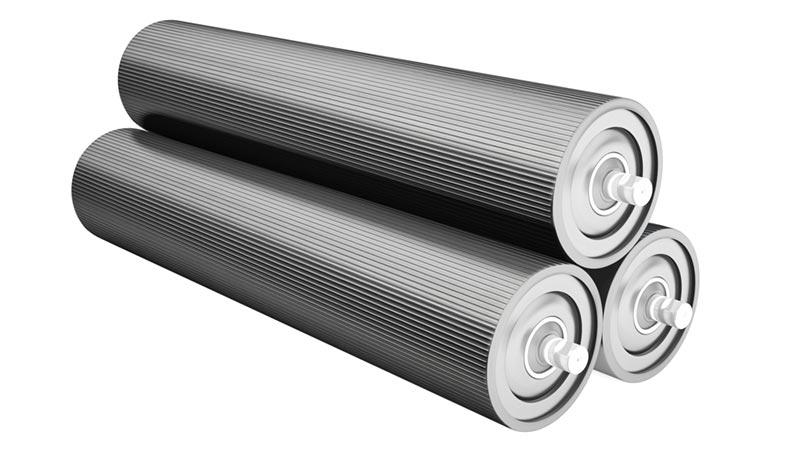
Dead shaft rollers
Dead shaft rollers have internal bearings located at the same place as a spinning roller that spins around a stationary shaft.
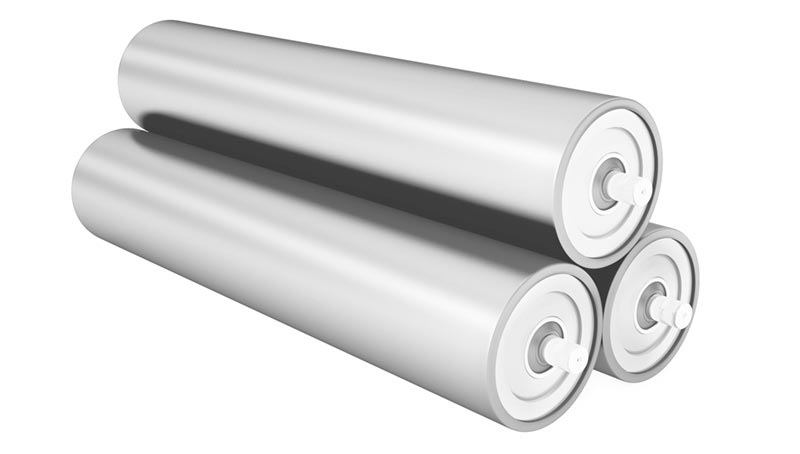
Cleaning rollers
Cleaning rollers are used to remove dirt, dust and other contaminants from different surfaces. They are highly specialized to each surface they clean.
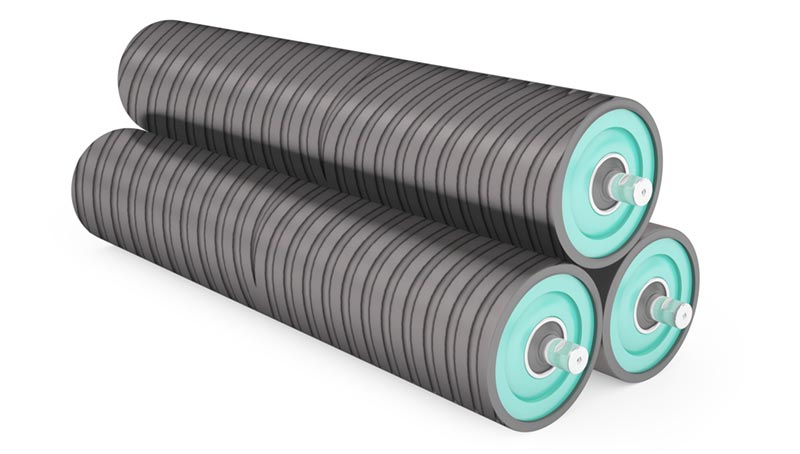
Spreader rollers
Spreader rollers, frequently machined with specialized groove designs, like herringbone, spiral, circumferential and lateral-fluted, are commonly used for webs spreading machinery and other spreading applications. In the case of web spreading machinery, spreader rollers stretch and spread the web to prevent and fix wrinkles.
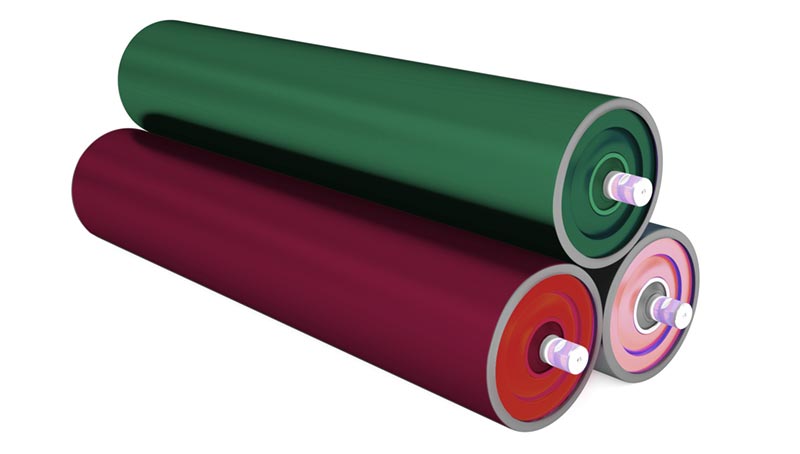
Urethane rollers
Urethane rollers, also known as polyurethane rollers, are made from a synthetic roller from polyurethane. They are inexpensive to produce, they have many great qualities, including: shock resistance, formability, durability, elasticity and strength. Urethane rollers are best for use in: data storage, packaging and assembling, printing, material handling, measurement systems and office equipment.

Standard shapes
Square Groove
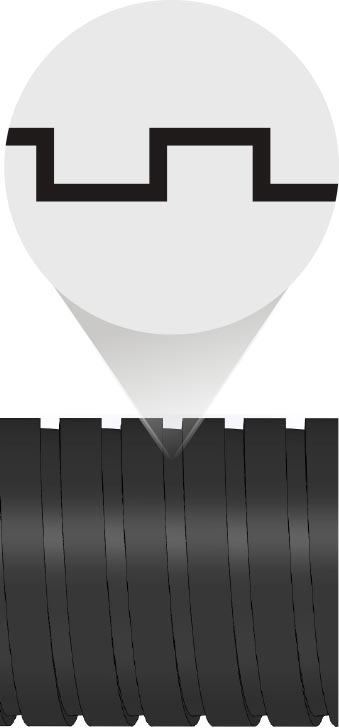
Applicable Groove pattern
• Vertical
• Horizontal
• Double Helical
• Worm
• Diamond
• Screw-thread
Trapezoidal
Groove
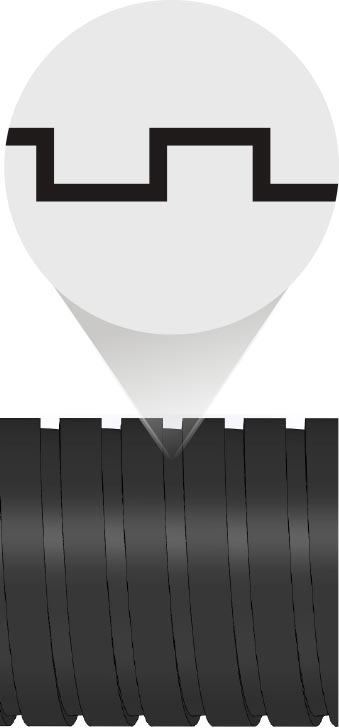
Applicable Groove pattern
• Vertical
• Horizontal
• Diamond
• Screw-thread
V Shape Groove
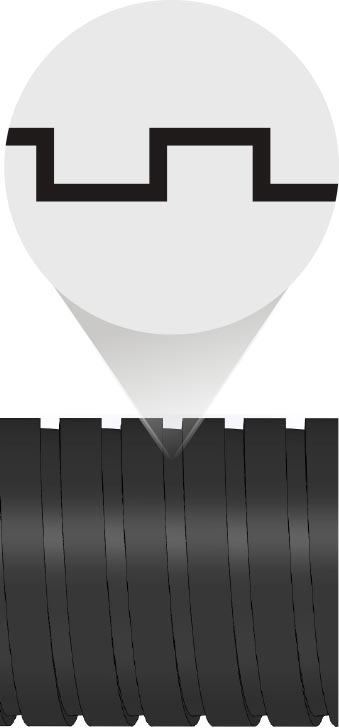
Applicable Groove pattern
• Screw-thread
Half Round Groove
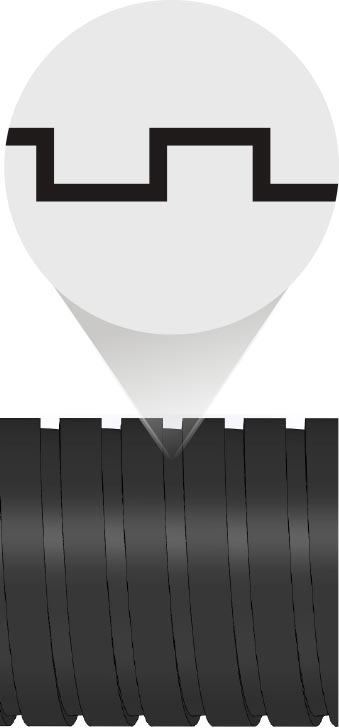
Applicable Groove pattern
• Vertical
• Screw-thread
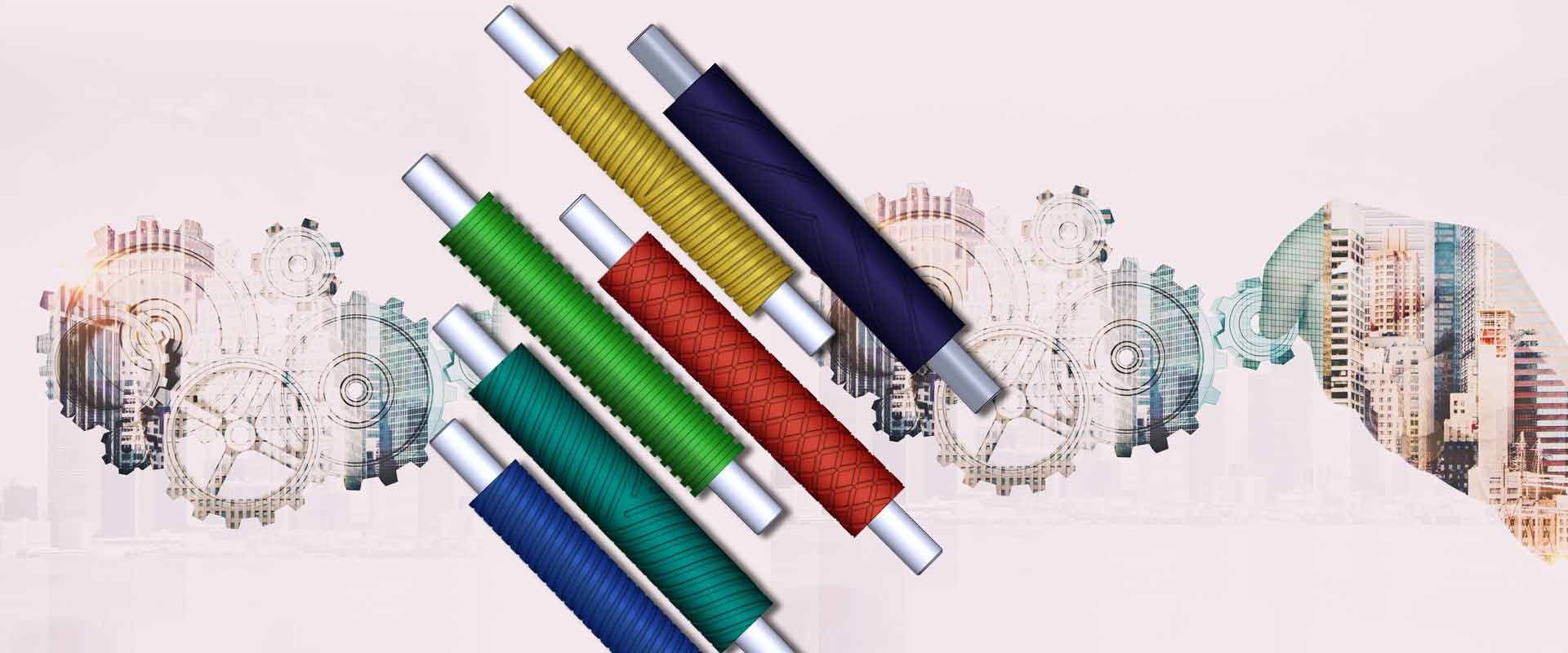
Grooving Types
Vertical Groove (Step And Plunge )

Ordering instruction
Required number of grooves
Applications
- Cardboard(Throw-in roller)
Purposes
- To emboss on plastics.
- To assist the heat release from polyurethane / rubber rollers.
- To apply softness of polyurethane / rubber rollers.
- To raise the coefficient of friction.
Horizontal groove (Ruling)

Ordering instruction
Required number of grooves
Applications
- Cardboard(Throw-in roller)
Purposes
- To prevent a belt slipping and meandering
- To emboss on plastics.
- To apply softness of polyurethane / rubber rollers.
- To raise the coefficient of friction.
Helical groove (Chevron)

Ordering instruction
Require number of grooves and an angle of the spiral.
Applications
- Belt sander for plywood
- Metal plate
Purposes
- To prevent a belt slipping and meandering
- To assist the heat release from polyurethane / rubber rollers.
Double helical groove (Herringbone)

Ordering instruction
Require number of grooves and an angle of the spiral.
Applications
- Belt sander for plywood
- Metal plate
Purposes
- To smooth out wrinkles in plastic films and papers.
- To prevent a belt slipping and meandering
- To assist the heat release from polyurethane / rubber rollers.
Worm groove (Spreader)

Ordering instruction
Require number of grooves and an angle of the spiral.
Applications
- Worm rollers for paper manufacturing
- Dyeing
- Guide rollers
Purposes
- To smooth out wrinkles in plastic films and papers.
- To prevent a belt slipping and meandering
- To assist the heat release from polyurethane / rubber rollers.
Diamond cut groove

Ordering instruction
Require number of grooves and an angle of the spiral.
Applications
- Grip rollers for cardboard
- Cloths
- Rollers for various kinds of film industry
Purposes
- To prevent a belt slipping and meandering
- To assist the heat release from polyurethane / rubber rollers.
- To improve contact stability with papers or plastic films.
Screw-thread groove (Helical)

Ordering instruction
Required number of grooves
Applications
- Coating rollers for plywood
- Metal plate
- Cardboard
Purposes
- To increase the amount of coating
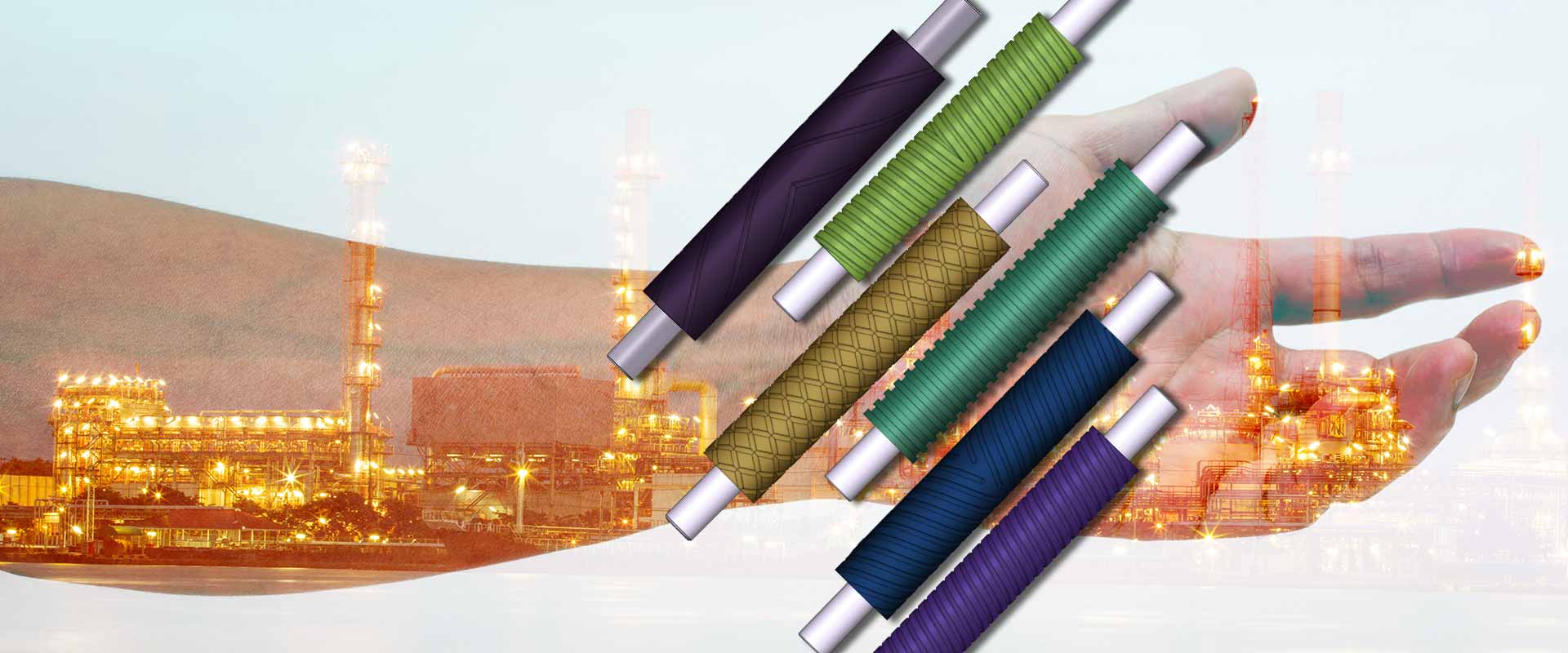
Grooving Options
1. Multi Layer
STEP & PLUNGE
RULING
CHEVRON
HERRING BONE
SPREADER
DIAMOND
HELICAL
2. Straight Grooved finish
STEP & PLUNGE
RULING
CHEVRON
HERRING BONE
SPREADER
DIAMOND
HELICAL
3. Concave Finish
STEP & PLUNGE
RULING
CHEVRON
HERRING BONE
SPREADER
DIAMOND
HELICAL
4. Convex finish
STEP & PLUNGE
RULING
CHEVRON
HERRING BONE
SPREADER
DIAMOND
HELICAL
5. Convex step finish
STEP & PLUNGE
RULING
CHEVRON
HERRING BONE
SPREADER
DIAMOND
HELICAL
6. Plain Grinding option
STEP & PLUNGE
RULING
CHEVRON
HERRING BONE
SPREADER
DIAMOND
HELICAL
Crown Processing
Crown height is the difference between the diameter of the roller center and the diameter of near the roller end (Generally 50 mm from the end)
The purposes of giving crown to rollers are:
- Correction of the roller deflection during operation. (Uniform contact)
- Making the most appropriate flow of the substrate such as cloth, plate and paper. (To avoid meandering)
It is better to give crown especially to the following rollers.
– The value of L/D (roller length / roller diameter) is relatively big.
– The pressure of the roller is relatively big.
Crown Types
STEP & PLUNGE
RULING
CHEVRON
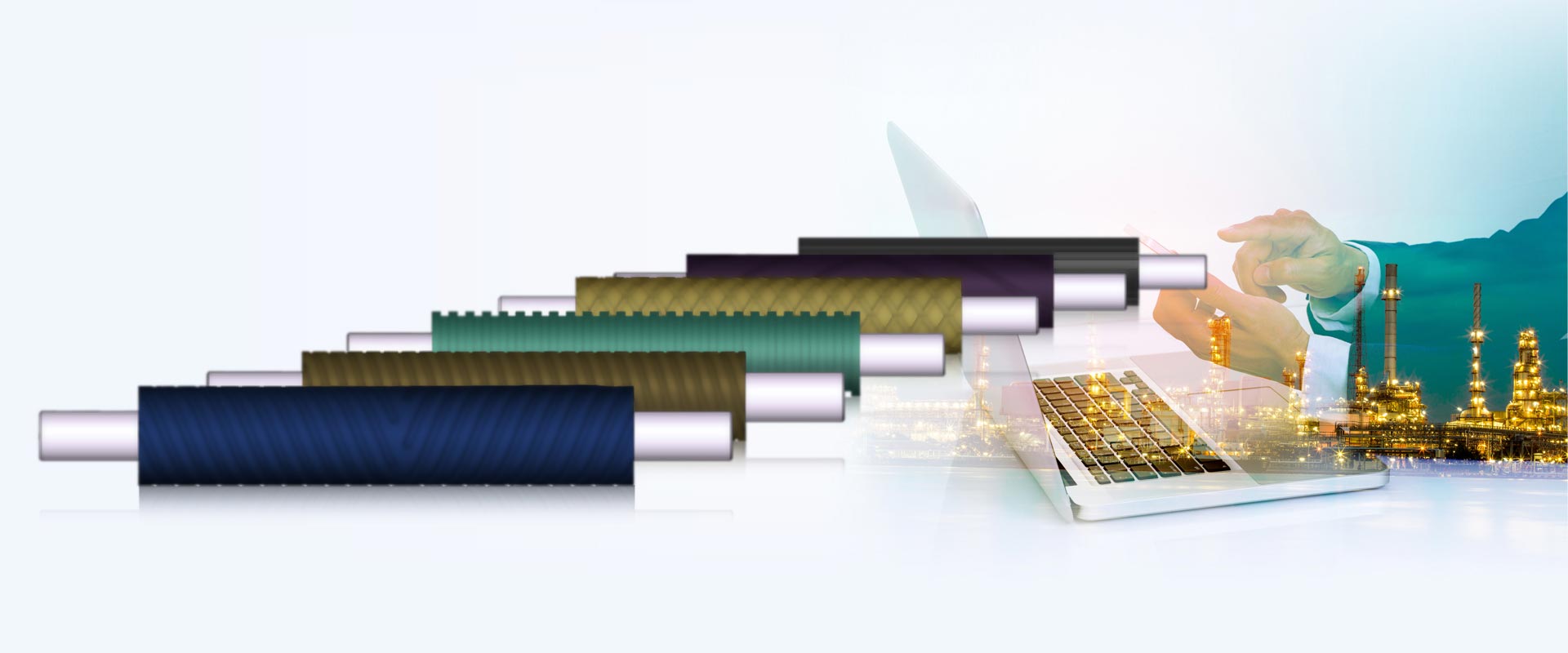
Care for Rollers
Polyurethane / Rubber rolls, just like every other component, has its limits and should be used as per the instructions. To learn how to extend the working life of your rolls, read the advice below.
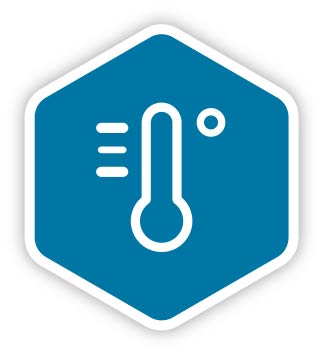
Temperature Regulation
High temperature is an enemy of polyurethane / rubber, regardless of the rubber type used for making rolls. Therefore, it is best to avoid rapid heating while using these rolls. You should also avoid rapid heating because the bonding adhesive usually has low heat resistance even lower than the rubber. If your application demands work under high temperature, we recommend you keep your roller temperatures under operating range by water cooling them.
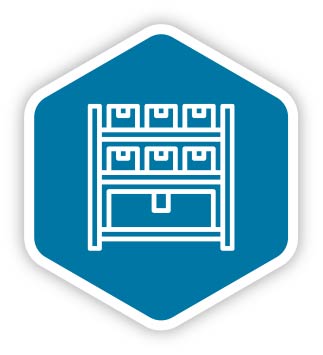
Storage
To avoid damage, you also need to store them properly. While storing a polyurethane / rubber roll, you must hold the shafts and stand them upright, so the rubber part does get exposed to other materials. Moreover, since rubber can be damaged by UV light, we recommend that you store your roller in a cool and dark place.
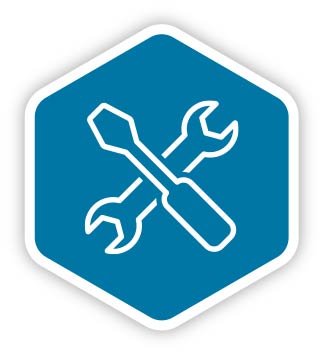
Maintenance Checks
During regular maintenance checks, you need to pay special attention to a number of roller parts. These include: ball bearings, axes and gears. Watch out for: worn-out ball bearings, bearings misaligned along their axes, overloaded gears, faulty gears, unbalanced rollers and deflected rollers.